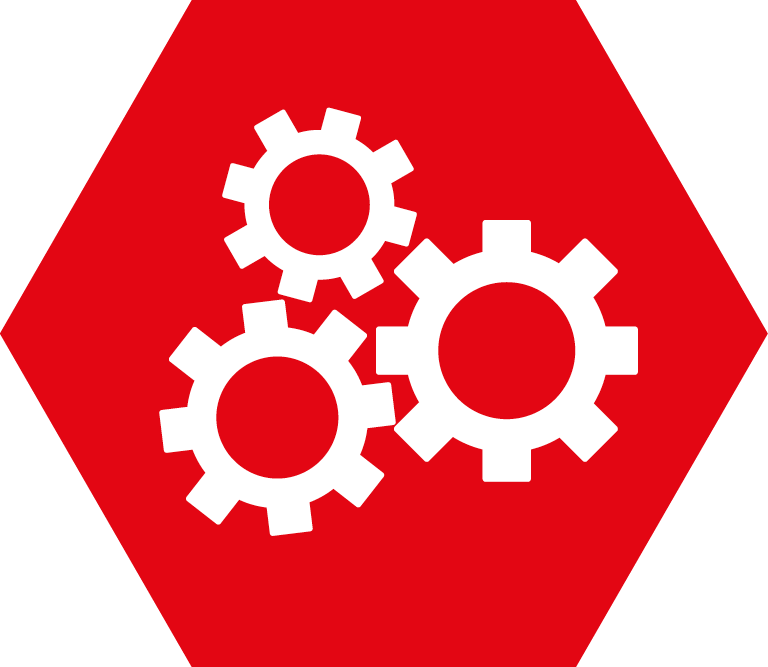
Automation technology
We tailor automation and innovation precisely to your needs: With Rotte’s expertise in intelligent automation technology, your company is one step ahead of the competition!
As a Rotte customer, you benefit from automation and innovation at the cutting edge of technology. More importantly, you gain access to a level of expertise that has already helped numerous businesses become more efficient and future-ready. As an experienced partner for customer-specific industrial automation, we develop tailored systems that meet your exact challenges—regardless of industry, task, or complexity. From partial automation of individual processes to fully connected Industry 4.0 systems, our solutions optimize your production sustainably. They help reduce production costs, minimize error sources, and stabilize internal processes to ensure your delivery performance.
Talk to our experts today about how we can enhance your operations with the latest technical innovations!
Your contact person
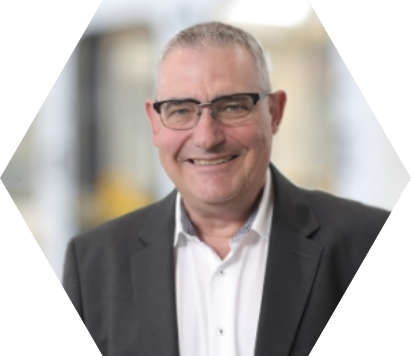
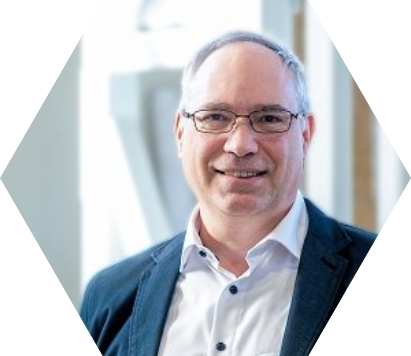

Daniel Bürgermeister
Technical sales & project planning
Automated Solutions for Your Production – Customized, Scalable, Efficient
In modern manufacturing environments, automation technologies are a key competitive advantage. They ensure consistent quality, reduce throughput times, increase process reliability in complex production steps, and boost flexibility in handling product variations. They also relieve employee workloads and improve workplace safety. Whether you’re active in automotive supply, the furniture industry, food processing, packaging technology, or the production of technical components—when you use a Rotte automation solution, you’re fully equipped for any application and ahead of the competition.
We deliver our innovative technologies as standalone units or as integrated modules for existing production systems—supporting your workflow whether in workpiece transport, assembly, packaging, or handling of delicate components.
Thanks to the modular design of our systems, you can expand capacity or adjust the level of automation as needed—an ideal advantage when your production needs to grow or adapt to new challenges. That’s why manufacturing companies across various industries trust Rotte for the development, implementation, and integration of their automation solutions.
Our services include:
- Automated Conveying: Energy-efficient conveyor systems with proven drive technology, tailored to your in-house logistics
- Intelligent Assembly: Robot- and cobot-assisted assembly stations at any desired level of automation
- Precise Packaging: Fully automated packaging solutions for a wide variety of product shapes and sizes
- Flexible Order Picking: Application-specific systems for automated picking of goods and components
- Reliable Sorting: Sorting systems with intelligent sensors and vision systems for rapid product classification
- Efficient Stacking: Space-saving palletizing and stacking systems for your end-of-line automation
- Integrated Handling: Gripping systems and handling technology for delicate or heavy parts
- Robot-Based Manufacturing: Flexible production cells with high repeatability and fast cycle times
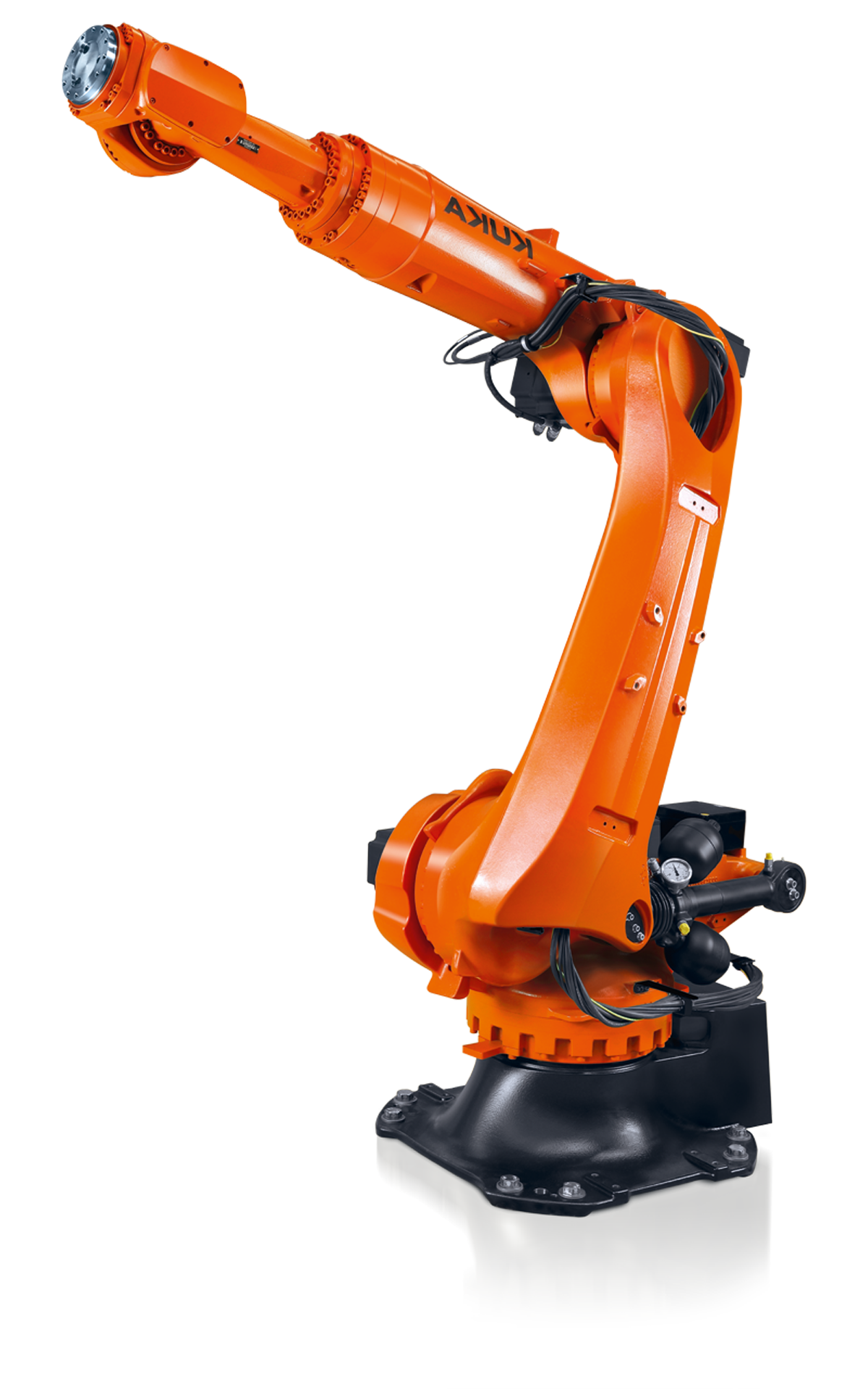
How Collaborative Robots Drive Your Production Forward
In many industries, the introduction of cobots is fundamentally changing the way work is done. From automotive and food to pharmaceuticals and electronics—the possibilities of collaborative robotics are virtually limitless. Rotte has gained extensive experience in this area and is ready to help you benefit from all that cobotics has to offer.
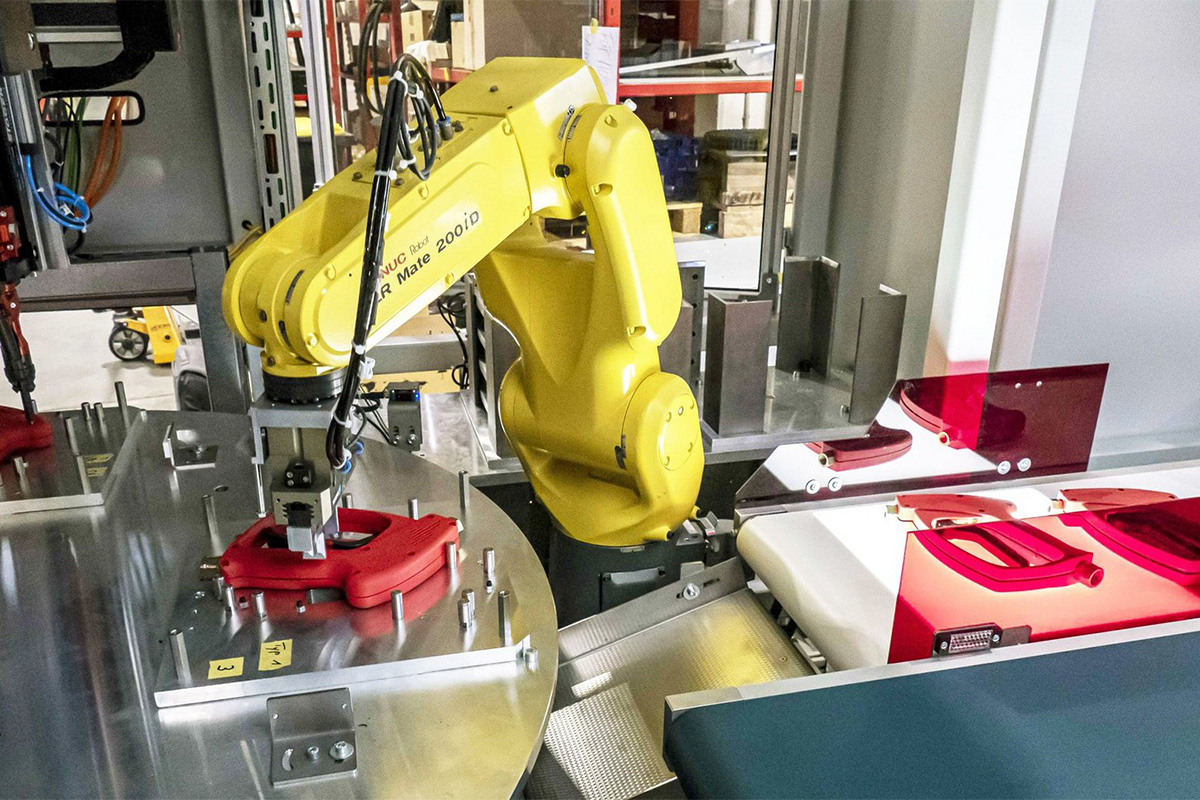
Robotics
Our robotics solutions range from compact robots for basic pick-and-place tasks to six-axis industrial robots for complex assembly and welding. We tailor the selection and design to your application—including custom-designed gripper systems and safety architecture. With flexible programming, high repeatability, and easy maintenance, we ensure reliable and scalable automation processes.
Industrial Vision Systems
Combined with high-resolution cameras and AI-based analysis software, our vision systems handle essential tasks such as quality control, component detection, and position verification. They identify faulty products during production, precisely position workpieces, and make your processes traceable—a crucial advantage in regulated industries like medical technology or automotive.
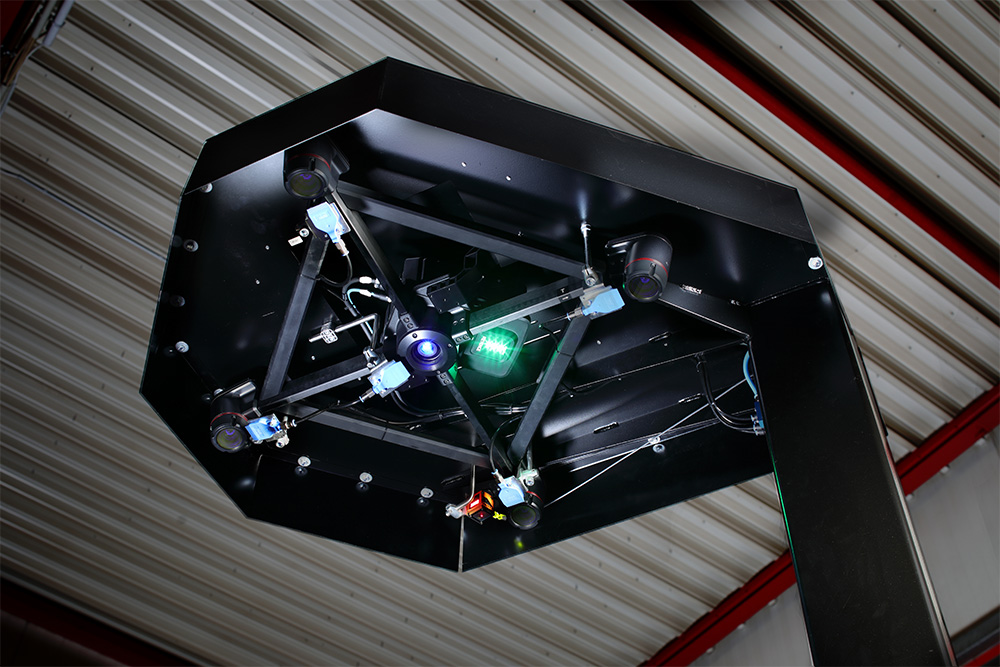
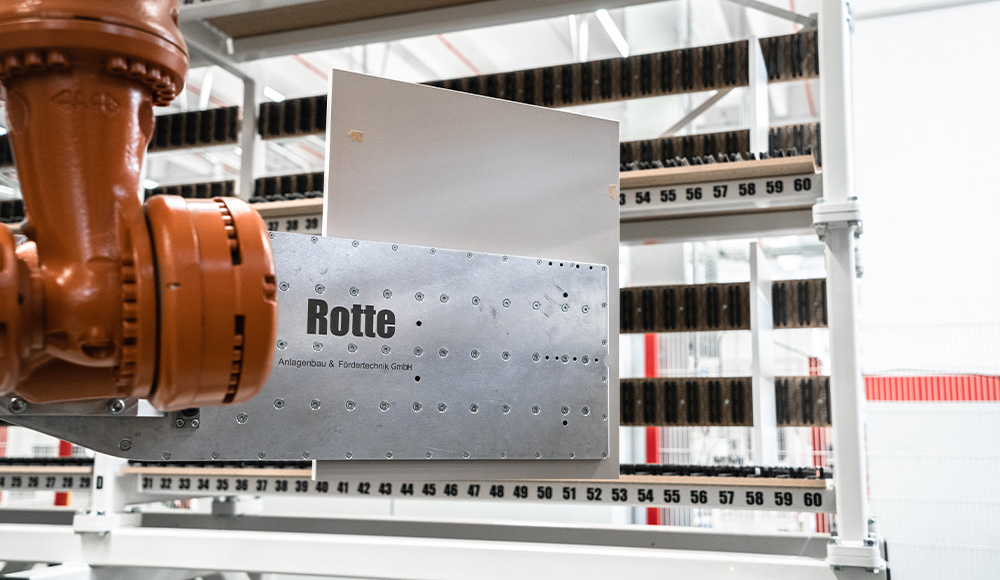
Cobots & Human-Machine Collaboration
In production environments where human involvement remains essential, our cobot solutions improve ergonomics, efficiency, and relieve physical strain. These collaborative robots handle repetitive, physically demanding, or precision-critical tasks, allowing your employees to focus on more value-adding activities. With modern safety features, easy programming, and minimal setup time, cobots can be seamlessly integrated into existing workstations—without protective barriers.
Smart Control Systems
The control system is the heart of every automation solution we deliver. Our PLC- and IPC-based controls are fully programmable, compatible with common fieldbus systems (like Profinet, EtherCAT, OPC UA), and enable full system connectivity. Supplemented with intuitive HMI interfaces, condition monitoring, and IoT integration, they create a digital twin of your production—for maximum transparency, control, and real-time responsiveness.
With our automation solutions, you can future-proof your operations against skilled labor shortages while reacting quickly to market shifts, rising demands, or new product variants.
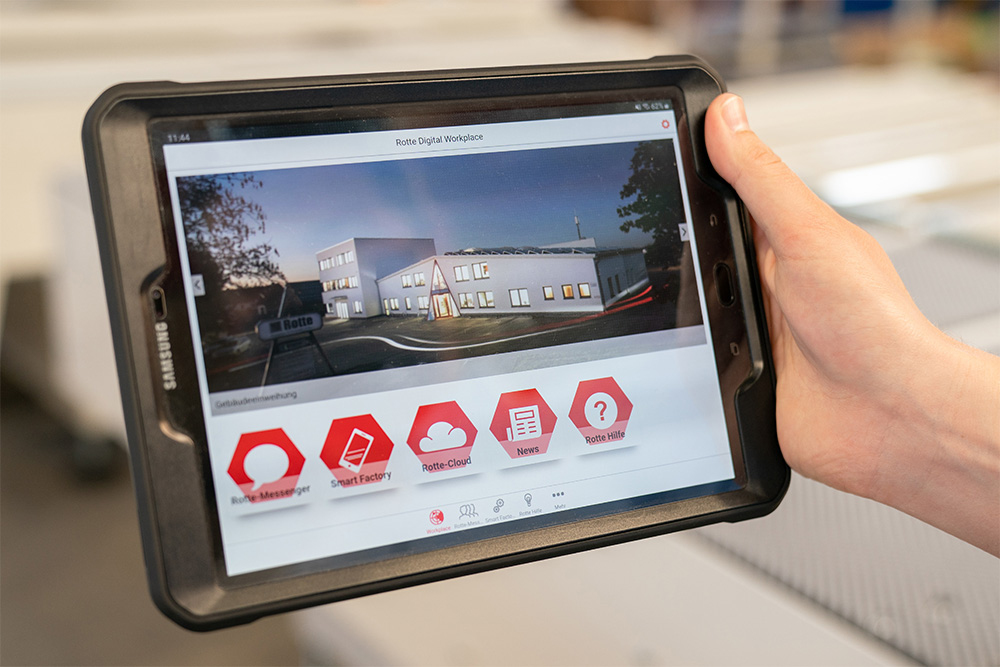
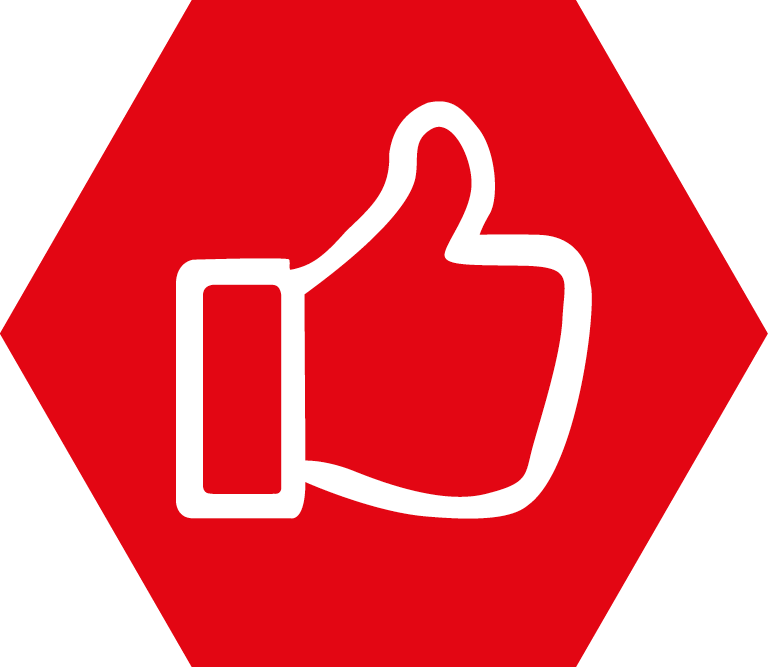
One Company, Many Advantages
Ulrich Rotte Anlagenbau & Fördertechnik GmbH is your specialist in custom machinery. In addition to our innovative solutions in special-purpose machinery and automation technology, you also benefit from a wide range of customer and after-sales services:
Your Advantages at a Glance:
- Decades of experience in special-purpose machinery
- Extensive know-how across all areas of automation technology
- High expertise in the latest technologies and applications for Industry 4.0
- All services from a single source—from development and design to manufacturing, assembly, commissioning, and regular on-site maintenance
- Optional training of your machine operators, technicians, and supervisors at your facility
- Mechanical engineering made in Germany – we design and manufacture exclusively in Germany
- Personalized customer support – you will always have a qualified contact person available
Our products
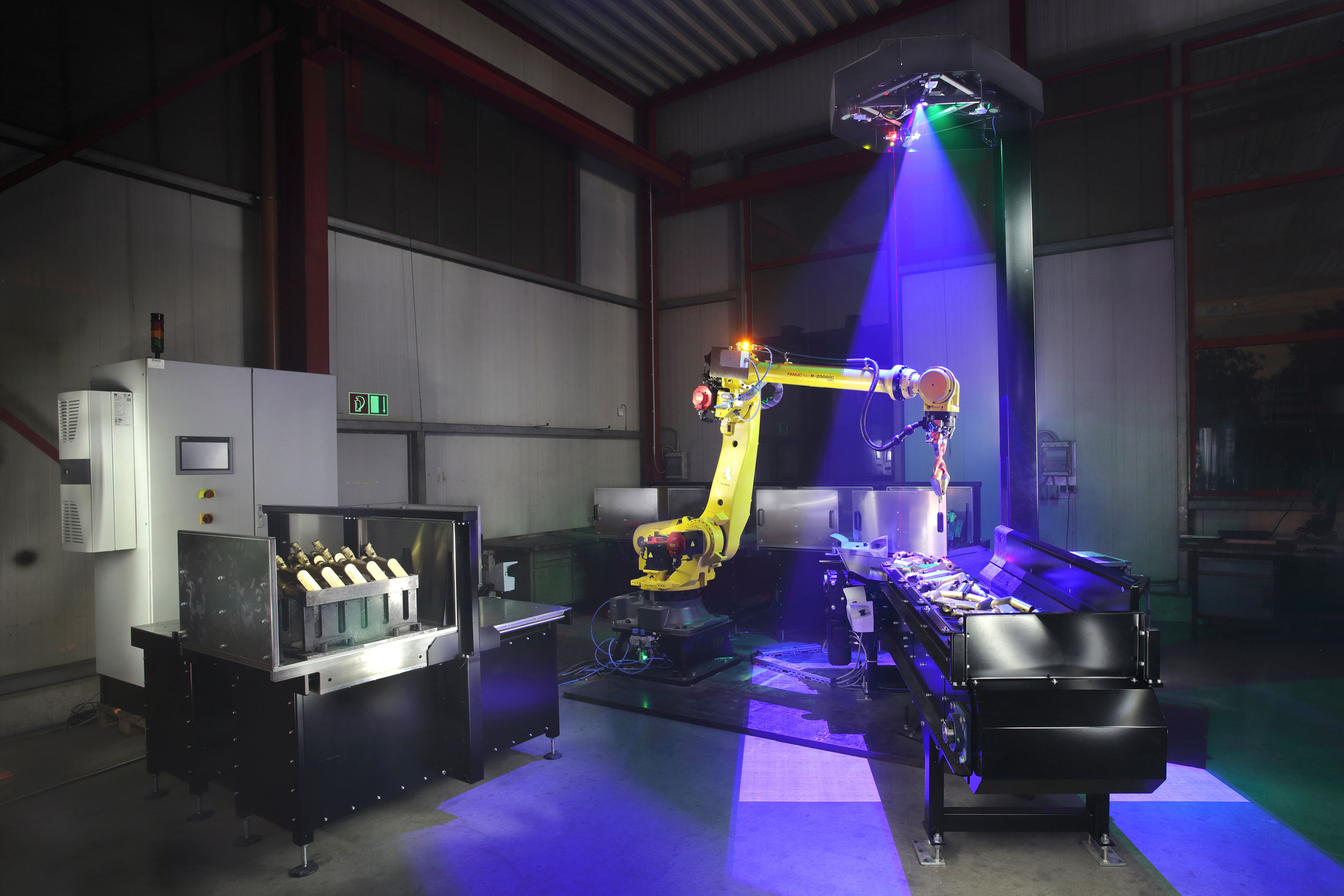
Bin Picking Cell CAMPGripX-1200
Precise and reliable Bin Picking In modern industrial production, every second counts. Companies are increasingly ...
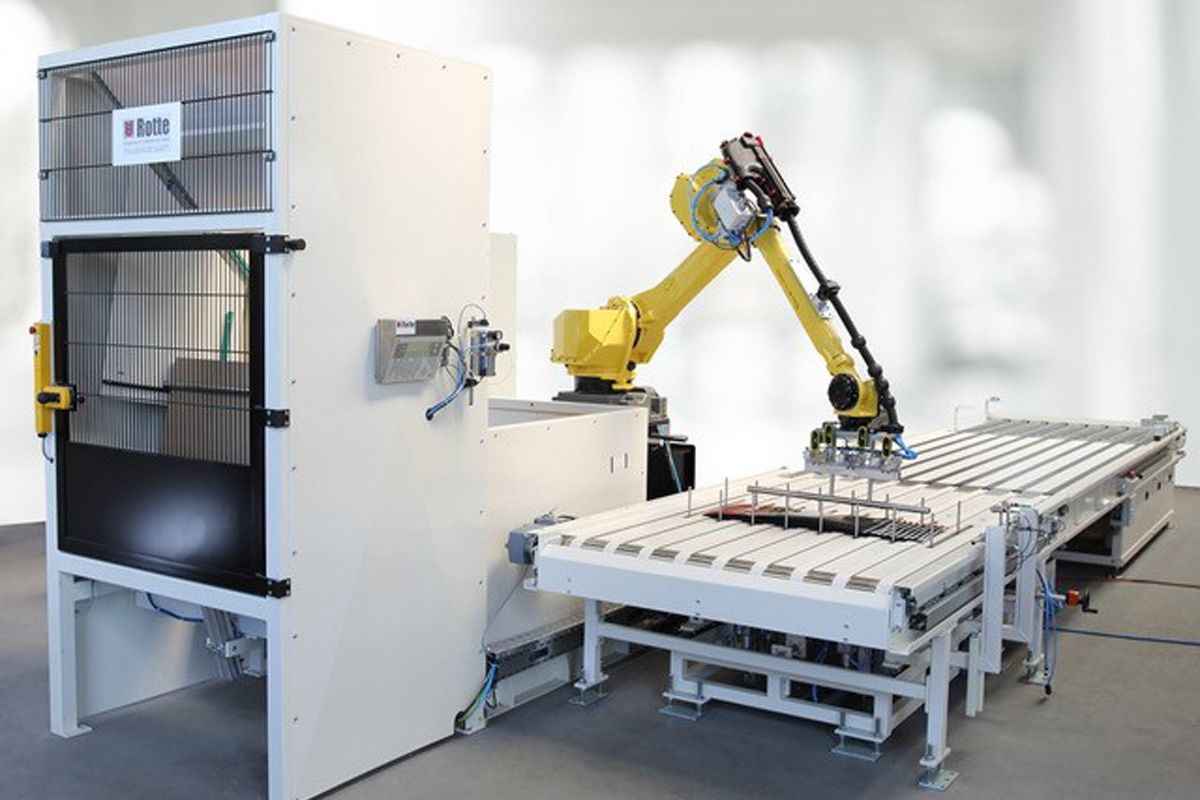
Bag and Pouch Packaging Machine
Efficient and Flexible Packaging Solutions Rotte develops fully customized packaging machines for pre-made bags and ...
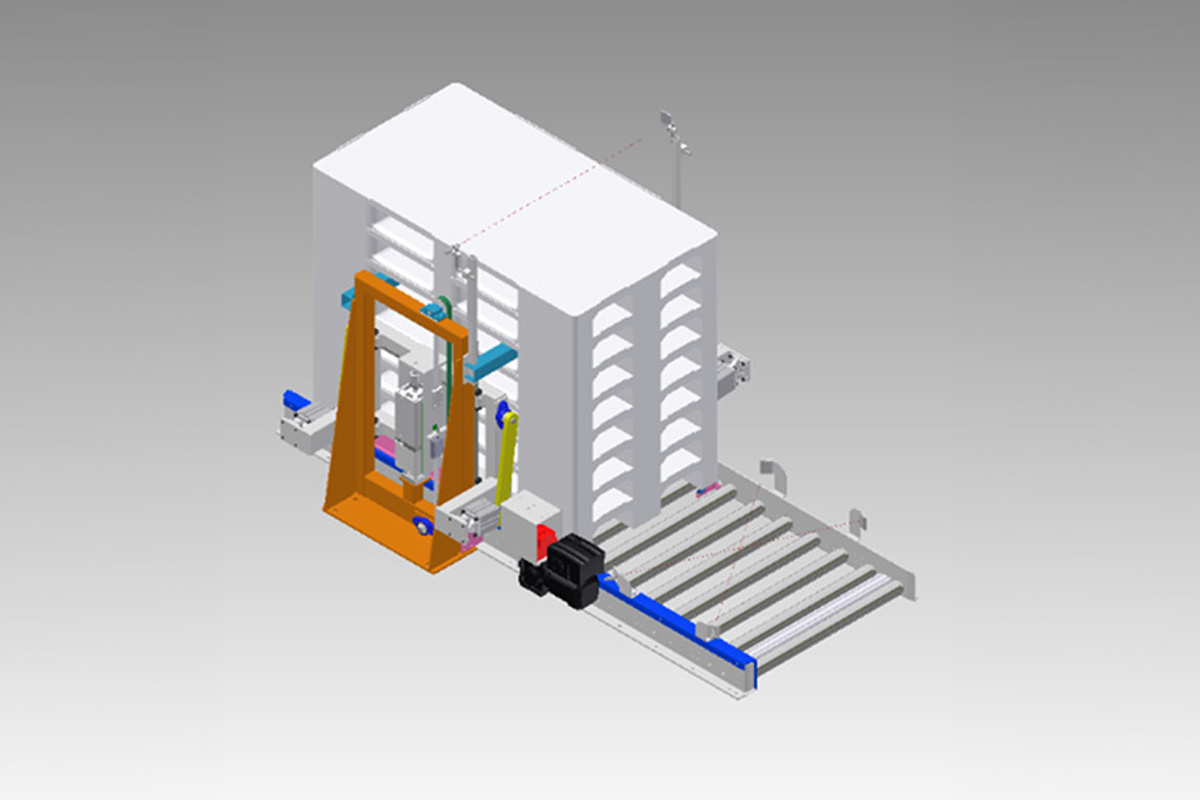
Automatic Pallet Magazine
Effortless Stacking and Destacking with Variable Capacity Efficient solutions for the automatic stacking and separation ...
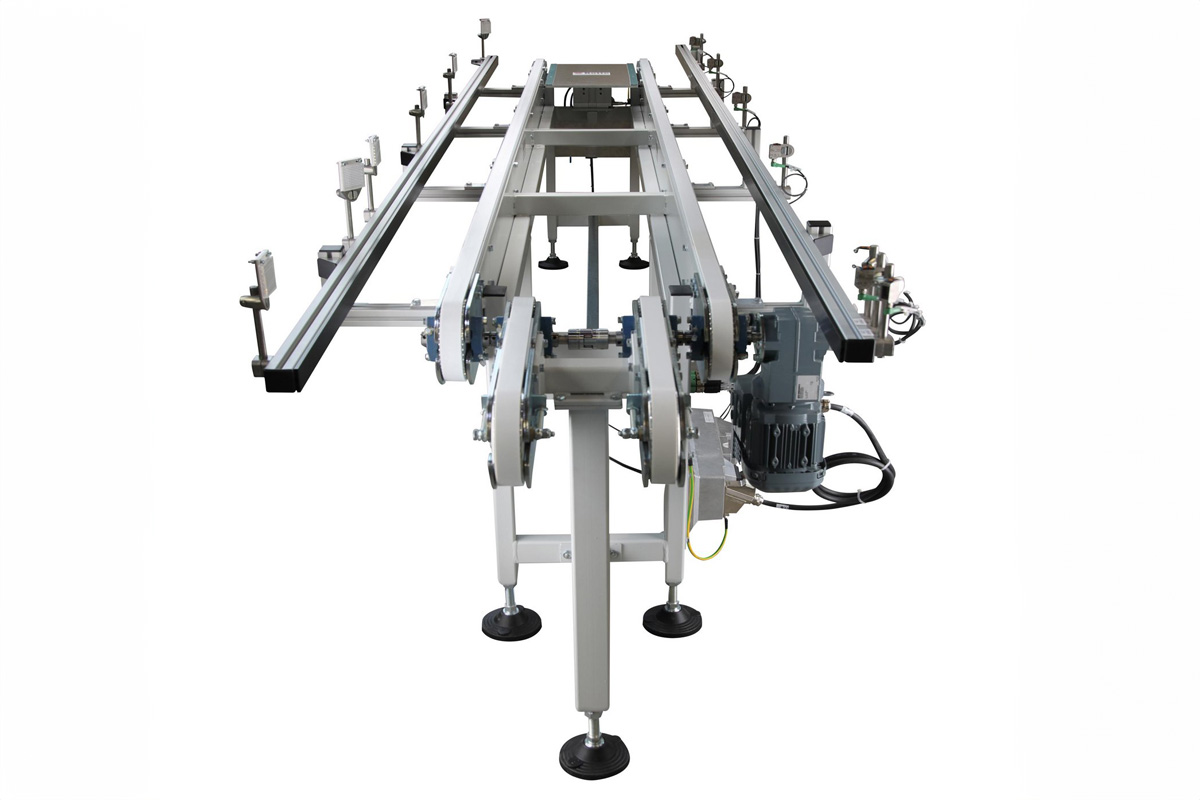
Belt Conveyors
Custom Conveyor Solutions for Your Production Efficient material flow is essential in modern production and ...
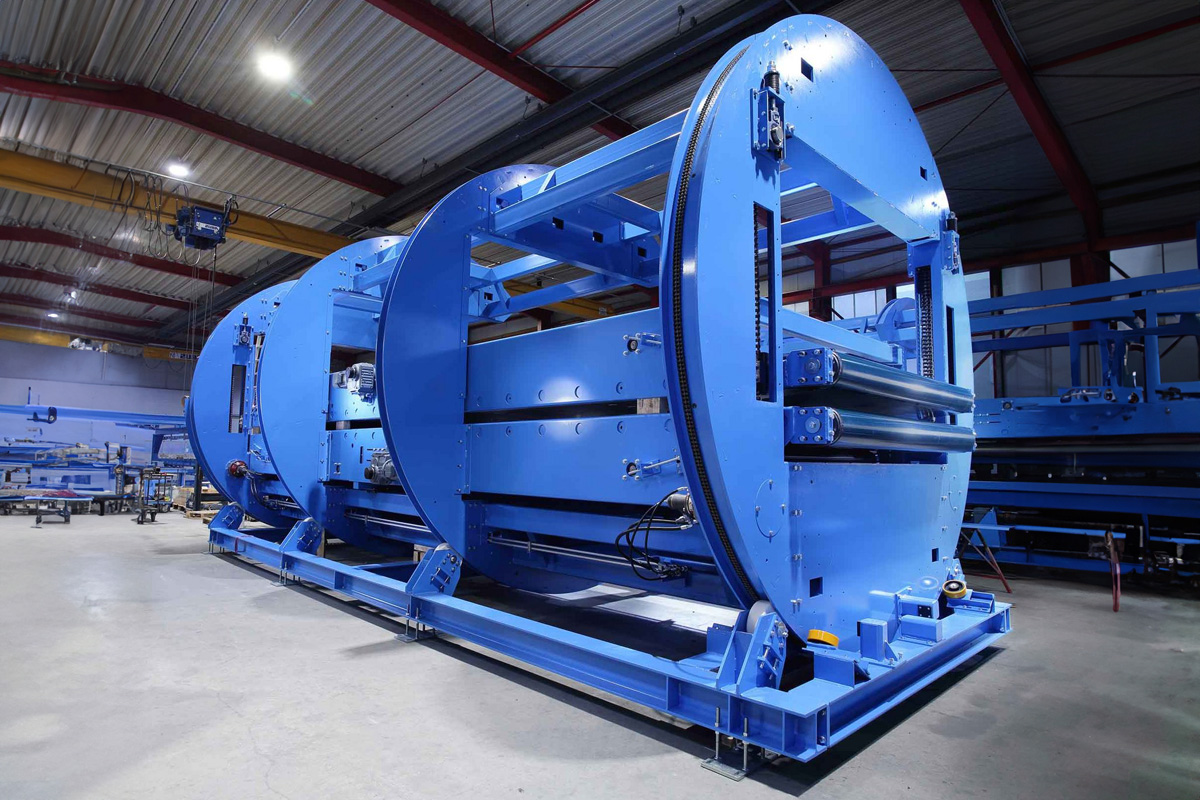
Drum Turner
When Everything Revolves Around Your Workpieces Turners for panels of all material types: In many ...
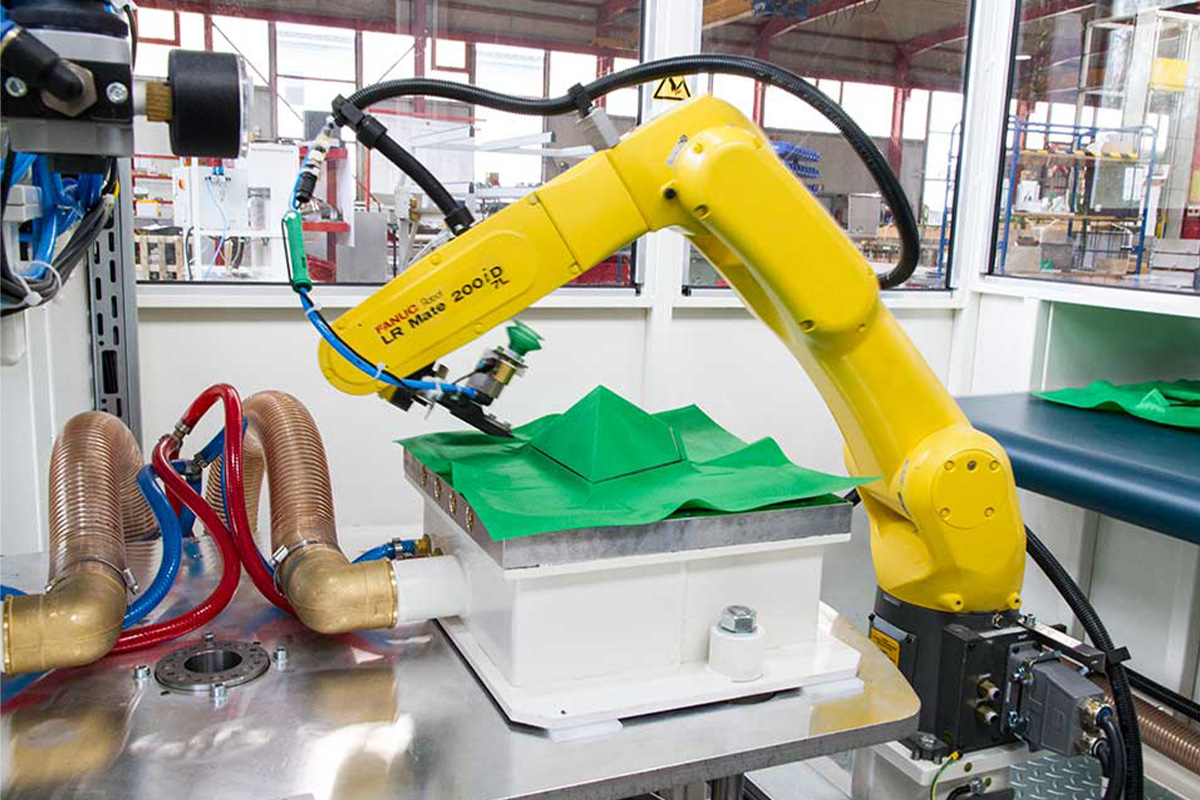
Thermoforming Machine
For the industrial processing of sealing fleece, filters, and technical fiber materials, Rotte offers high-precision ...
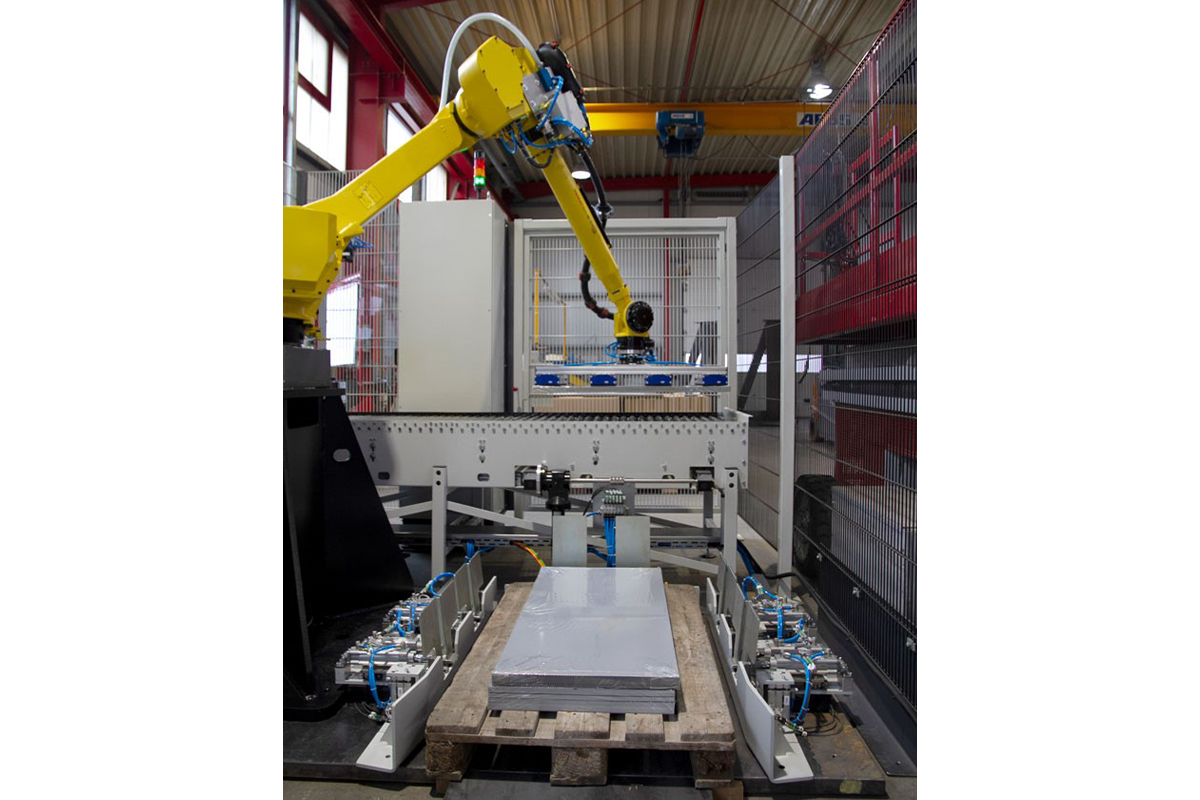
Loading and Stacking Robots
Smart Automation for Precise and Efficient Stacking In today’s industrial environments—with their complex production and ...
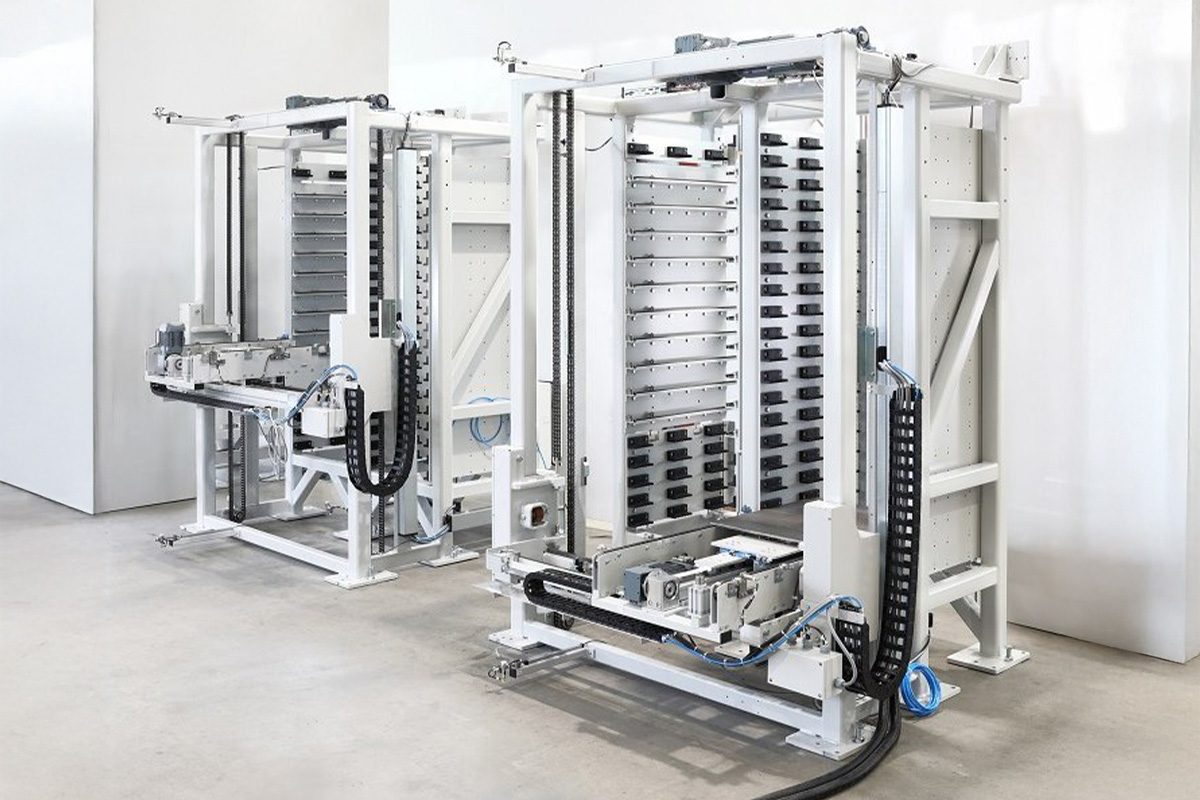
Automated Storage Systems for Multi-Daylight Presses
In high-output production processes involving multi-daylight presses, efficient storage and automation solutions are essential for ...
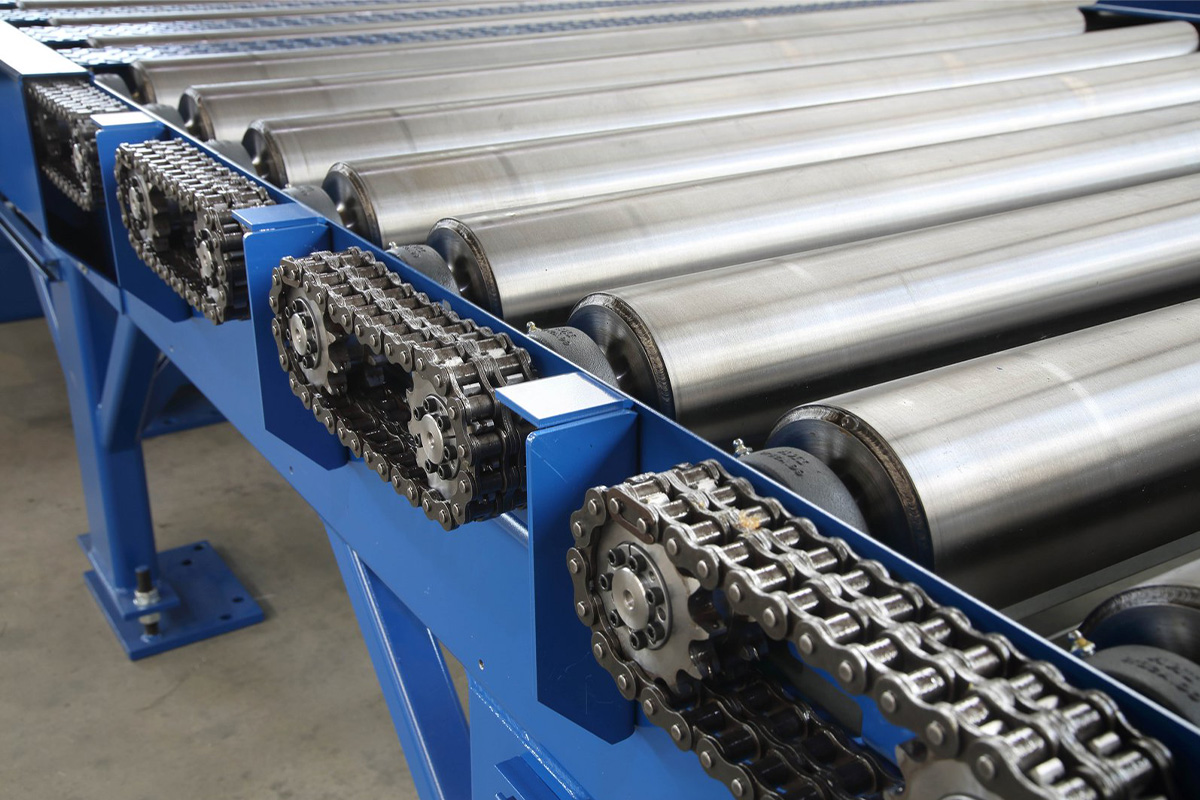
Heavy-Duty Roller Conveyors
Heavy-duty roller conveyors from Rotte are an optional yet integral component of our complete solutions ...
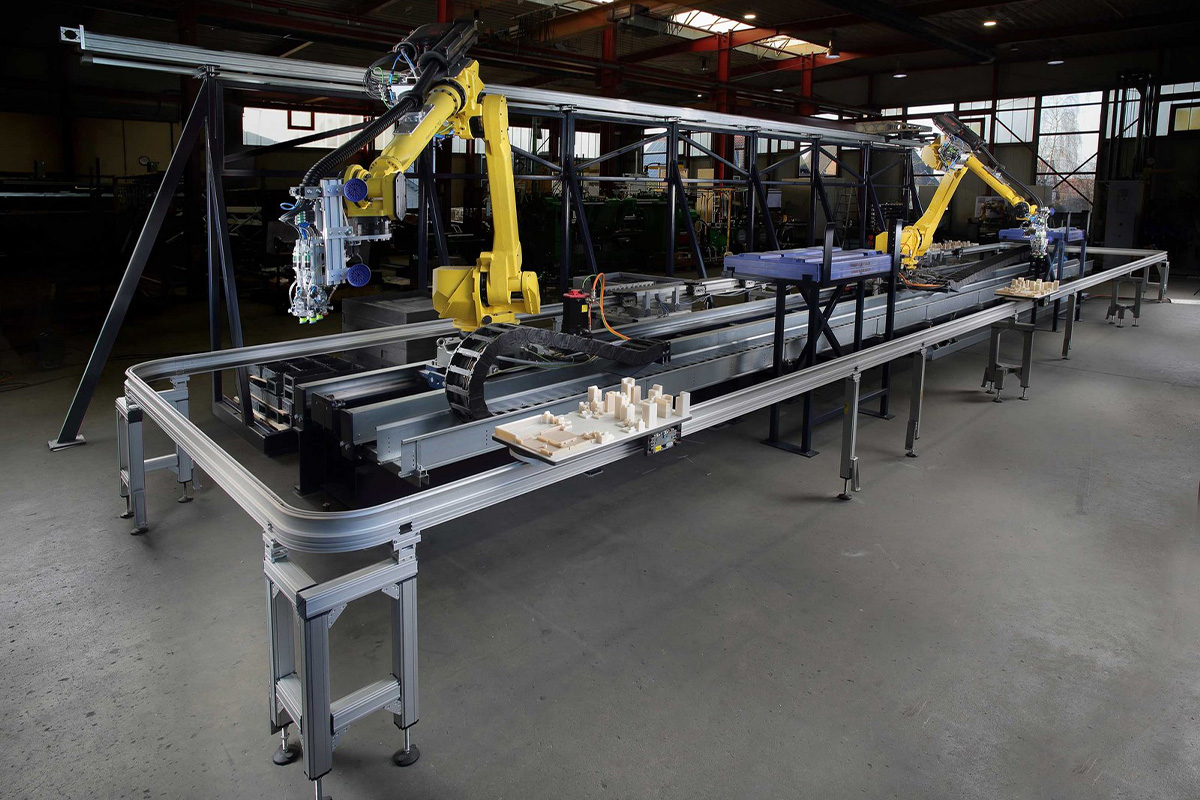
Picking Robots
Robotic Order Picking: Efficient Automation for Precise and Flexible Logistics with Customized Picking Robots In ...