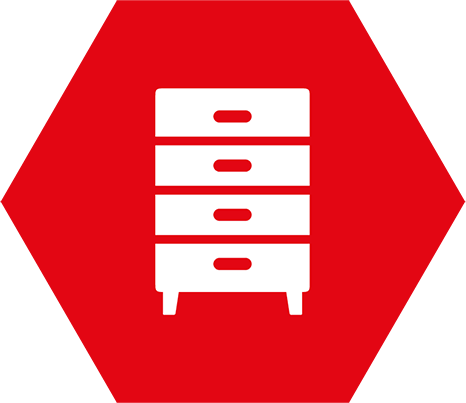
Wood and Furniture Industry
Automation Solutions for Greater Efficiency and Profitability in the Furniture Industry
The furniture industry combines traditional craftsmanship with highly modern serial production. At the same time, demands for flexibility, product quality, and delivery times are rising—especially for customized products and diverse product series. Rotte supports companies in the wood processing industry with tailor-made automation and special-purpose machine solutions that make all stages of furniture production more efficient, safer, and more cost-effective.
Whether for manufacturing furniture parts, processing panel materials, or final assembly—our systems are designed to integrate seamlessly into existing processes while dynamically adapting to new requirements. With our expertise in robotics, vision systems, control technology, and conveyor equipment, we deliver holistic, high-performance system concepts that meet the demanding standards of modern furniture production.
Get in touch with us today for a free and non-binding consultation!
Your contact person
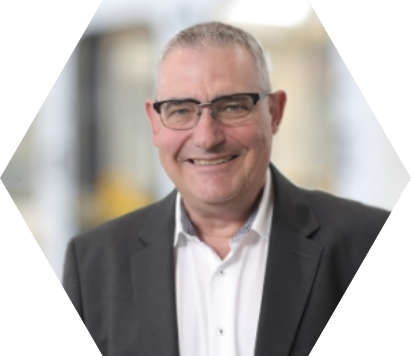
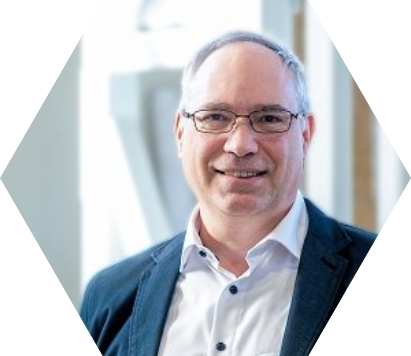

Daniel Bürgermeister
Technical sales & project planning
Custom Automation Solutions for the Wood Processing Industry
Processing wood and wood-based materials requires high precision—while also meeting fast cycle times, handling delicate surfaces, and accounting for often unpredictable material characteristics. With our custom-designed machines and systems, we offer the wood processing industry reliable technology for the automated handling of wood panels, profiles, veneers, and components of all kinds.
All of our systems can be easily integrated into existing production structures and precisely adapted to your operational workflows.
Our systems handle tasks such as:
- Automated feeding and separation of panels and profiles
- Machining steps such as milling, drilling, sawing, and sanding within coordinated production cells
- Formatting and positioning of large workpieces using robot-assisted handling
- Assembly and joining of components and subassemblies
- Conveying, sorting, and stacking using material-friendly technologies
- Integrated quality control via industrial image processing
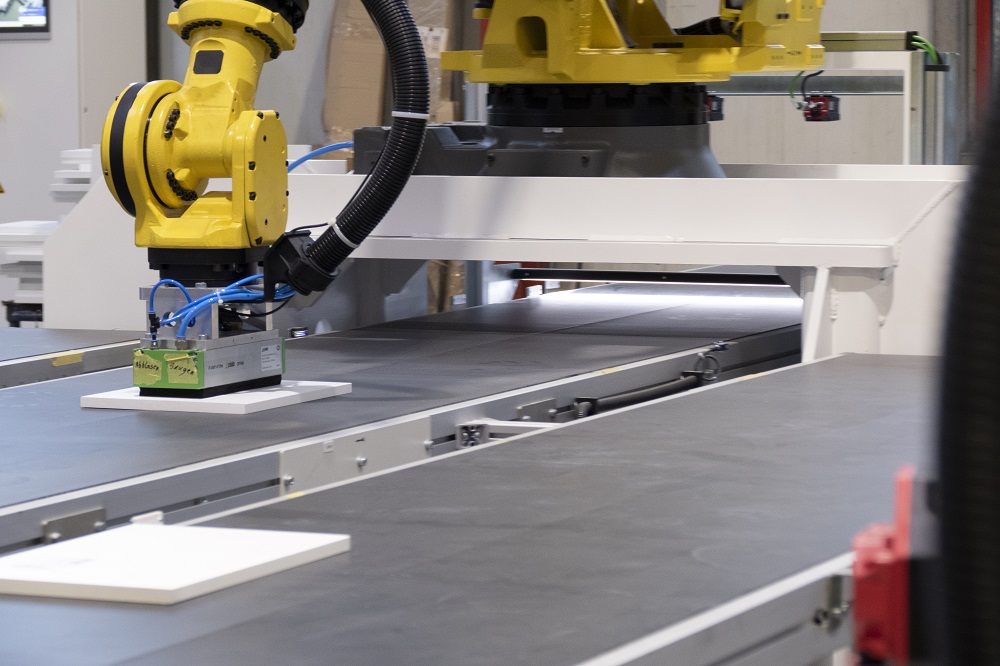
Robotic Solutions for Flexible and Efficient Furniture Production
The increasing variety of products in furniture manufacturing requires automation solutions that are not only fast but also smart. With our experience in integrating robotics and industrial vision technology, we implement highly flexible production systems that automatically adapt to different components and product formats.
Our solutions in the furniture industry include, among others, pick-and-place robots for precise placement of parts, handles, fittings, or connectors; robot-assisted assembly cells for cabinet and drawer box assembly; glue application and screw fastening; and vision systems for surface inspection, edge detection, or part identification. We also offer various solutions for the automated palletizing and order picking of furniture components after production.
Make your production workflows precisely reproducible and quickly adjustable when needed—regardless of whether you’re producing small batches or large volumes.
Rotte Automates the Furniture Industry of Tomorrow
The production of furniture and wood components requires more than just mechanical processes. It calls for smart, integrated solutions that fit seamlessly into complex production environments. With our experience in special-purpose machine construction across many industries, we’re happy to develop not only individual systems but also complete turnkey production lines for your company.
Whether you manufacture bedroom furniture, bathroom furniture, living room furniture, or kitchen cabinets—with Rotte as your partner, you’ll make your operations more innovative and competitive. Talk to us!
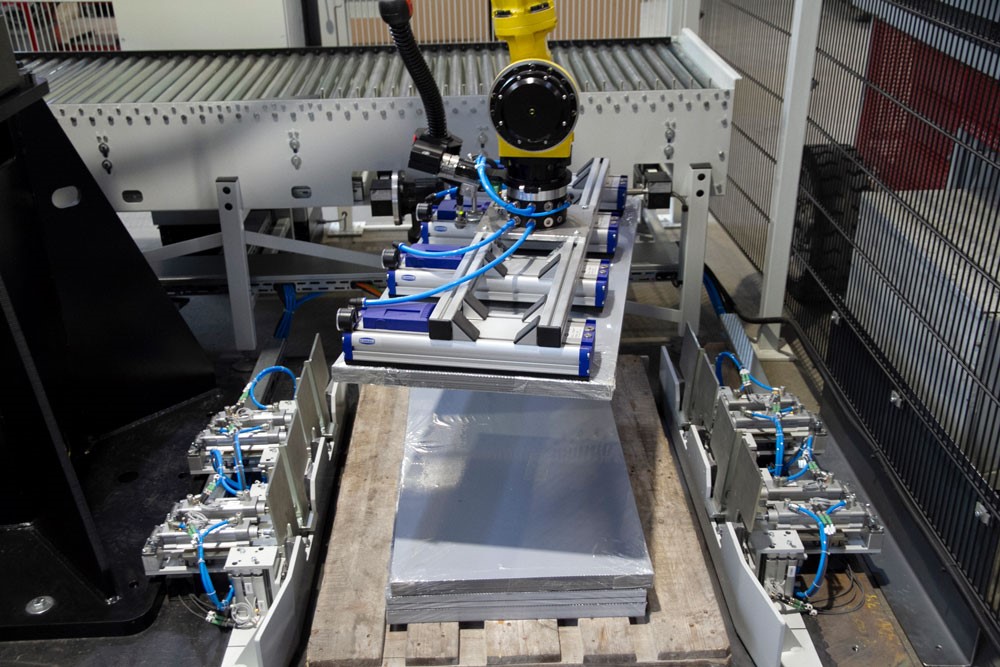
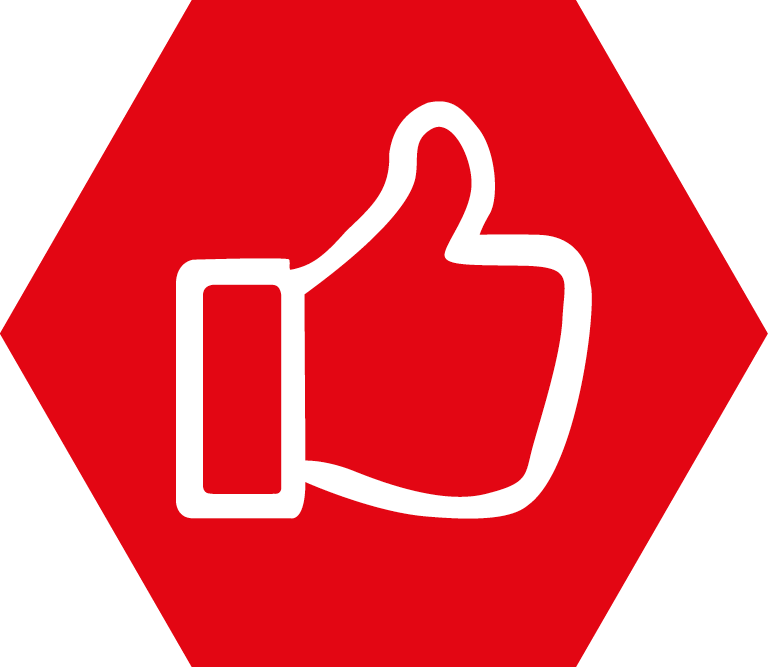
One Company, Many Advantages
Ulrich Rotte Anlagenbau & Fördertechnik GmbH is your specialist in custom machinery. In addition to our innovative solutions in special-purpose machinery and automation technology, you also benefit from a wide range of customer and after-sales services:
Your Advantages at a Glance:
- Decades of experience in special-purpose machinery
- Extensive know-how across all areas of automation technology
- High expertise in the latest technologies and applications for Industry 4.0
- All services from a single source—from development and design to manufacturing, assembly, commissioning, and regular on-site maintenance
- Optional training of your machine operators, technicians, and supervisors at your facility
- Mechanical engineering made in Germany – we design and manufacture exclusively in Germany
- Personalized customer support – you will always have a qualified contact person available
Our products
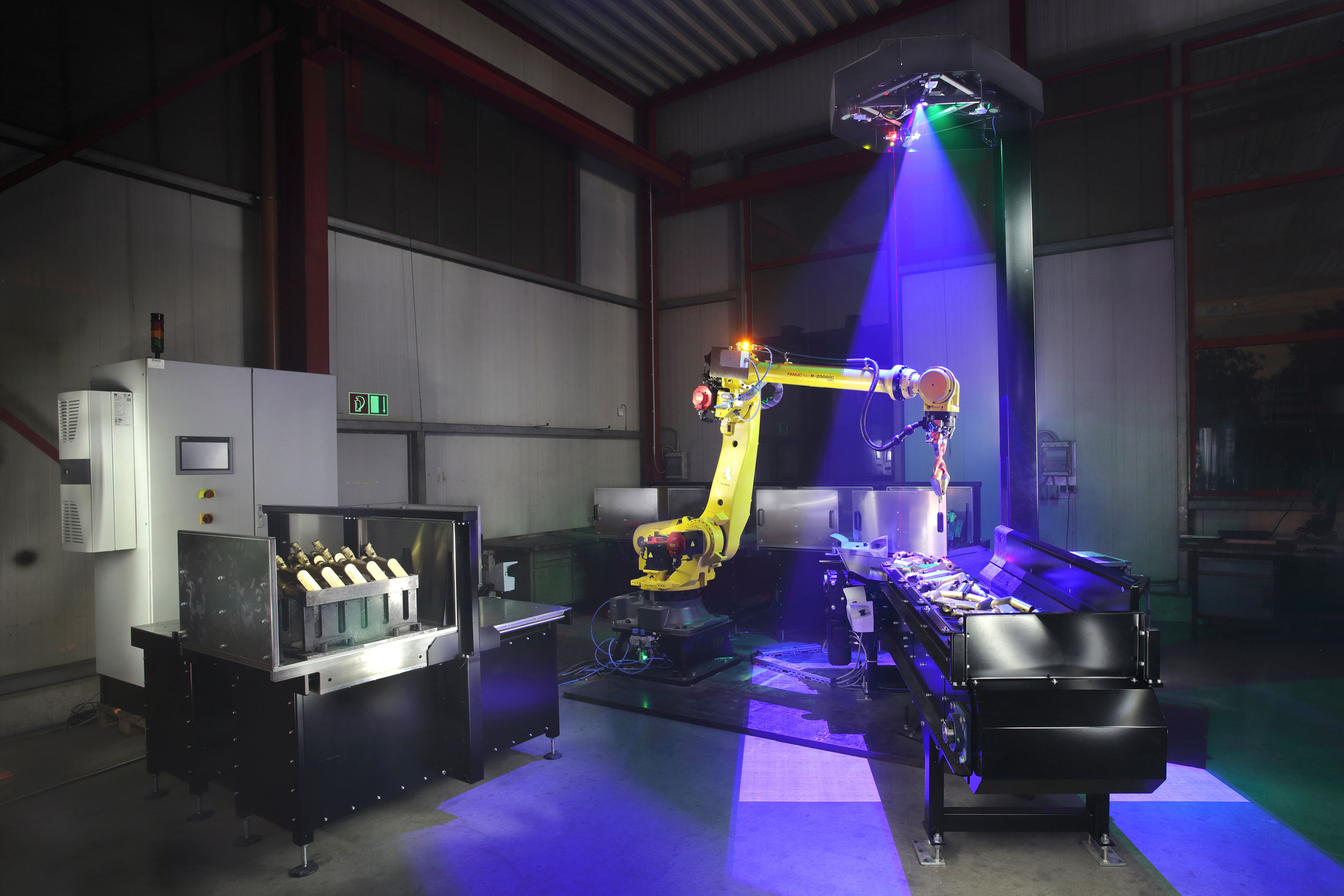
Bin Picking Cell CAMPGripX-1200
Precise and reliable Bin Picking In modern industrial production, every second counts. Companies are increasingly ...
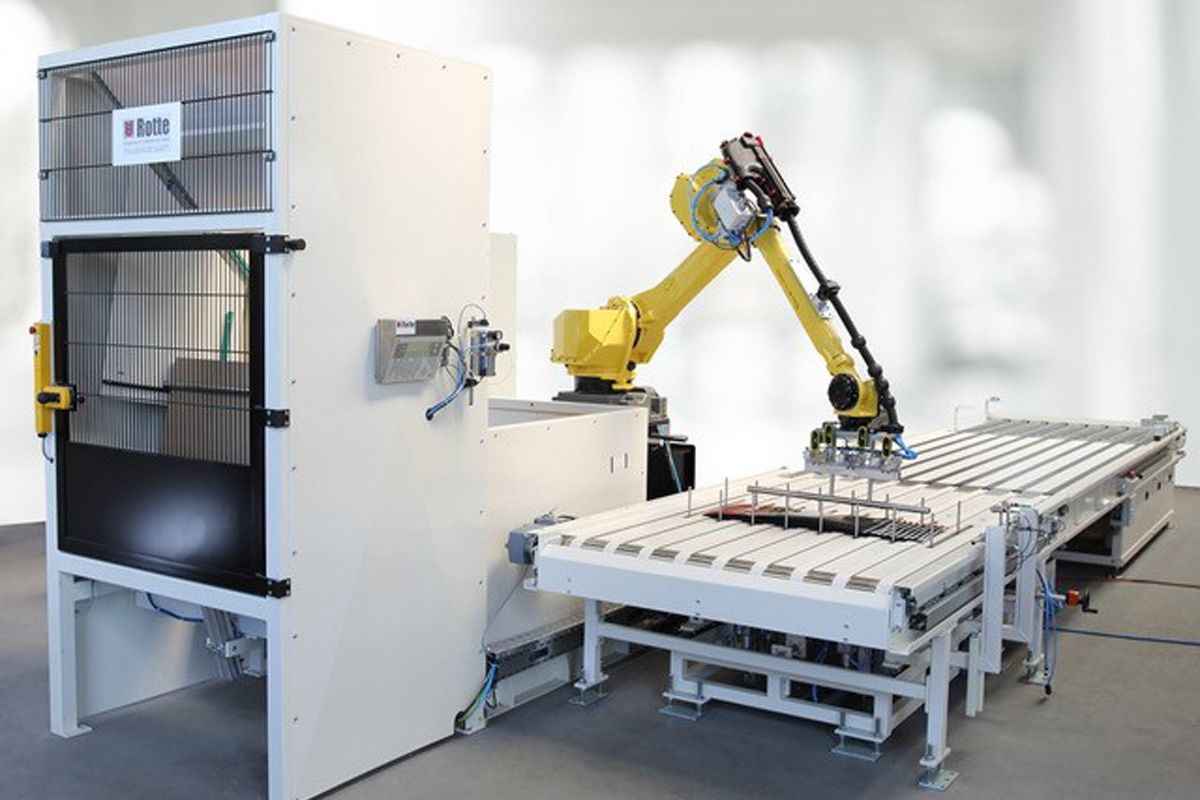
Bag and Pouch Packaging Machine
Efficient and Flexible Packaging Solutions Rotte develops fully customized packaging machines for pre-made bags and ...
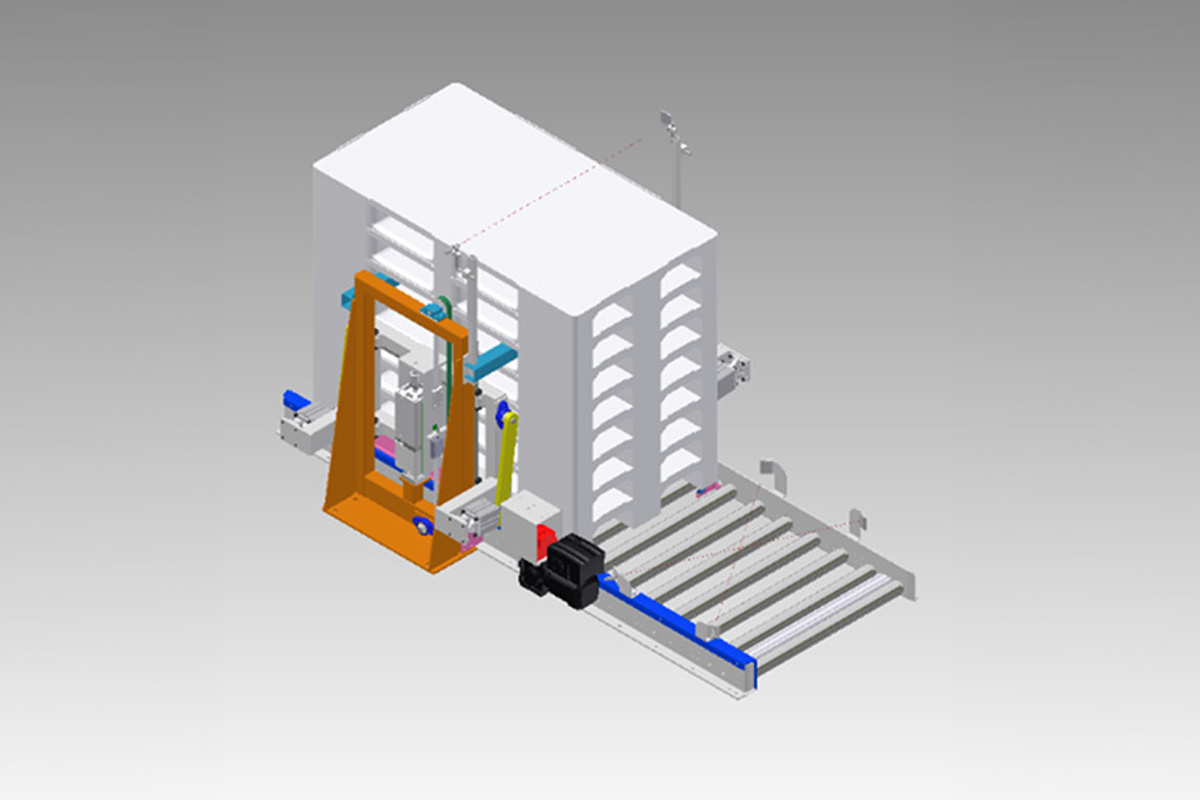
Automatic Pallet Magazine
Effortless Stacking and Destacking with Variable Capacity Efficient solutions for the automatic stacking and separation ...
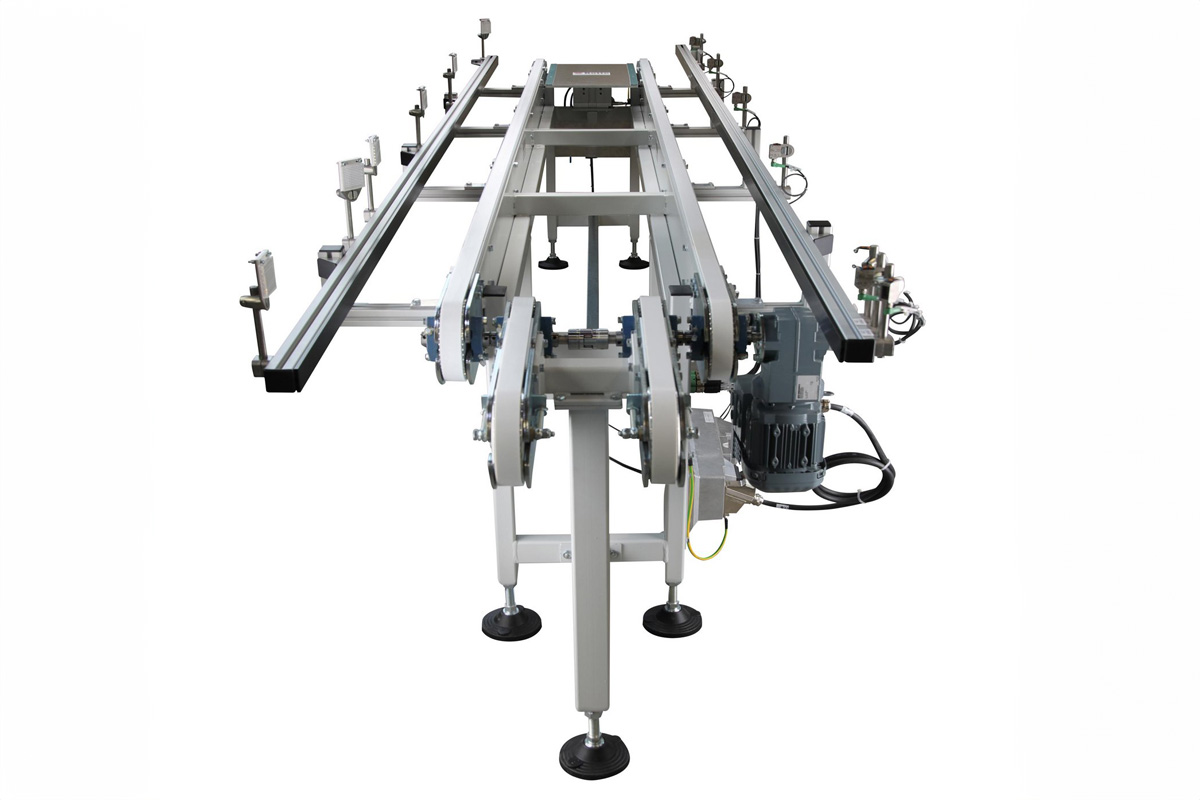
Belt Conveyors
Custom Conveyor Solutions for Your Production Efficient material flow is essential in modern production and ...
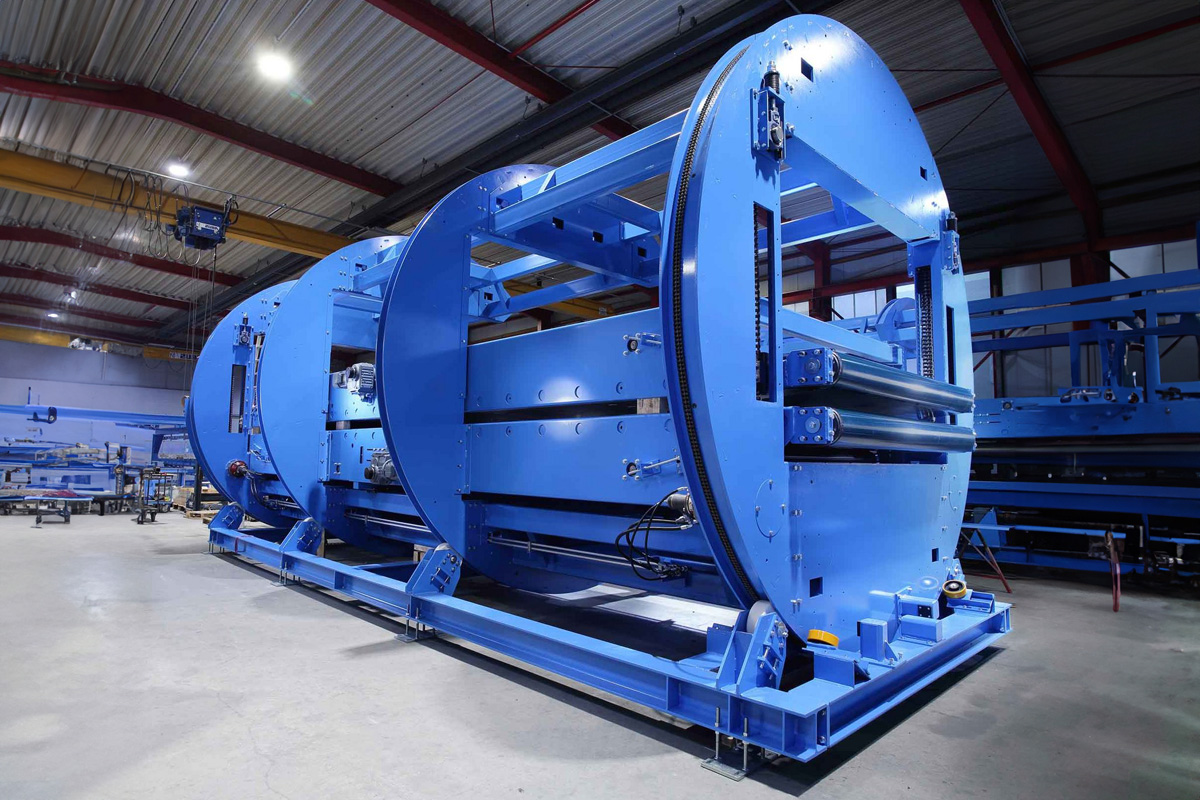
Drum Turner
When Everything Revolves Around Your Workpieces Turners for panels of all material types: In many ...
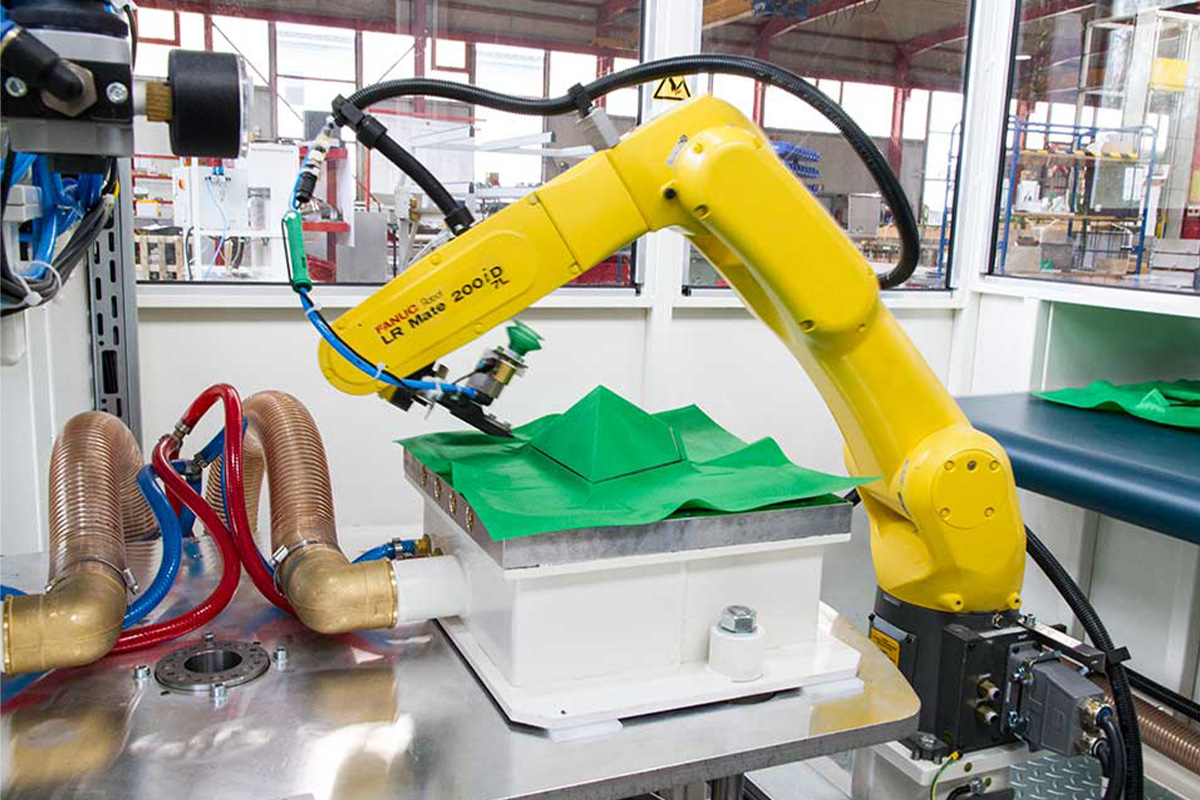
Thermoforming Machine
For the industrial processing of sealing fleece, filters, and technical fiber materials, Rotte offers high-precision ...
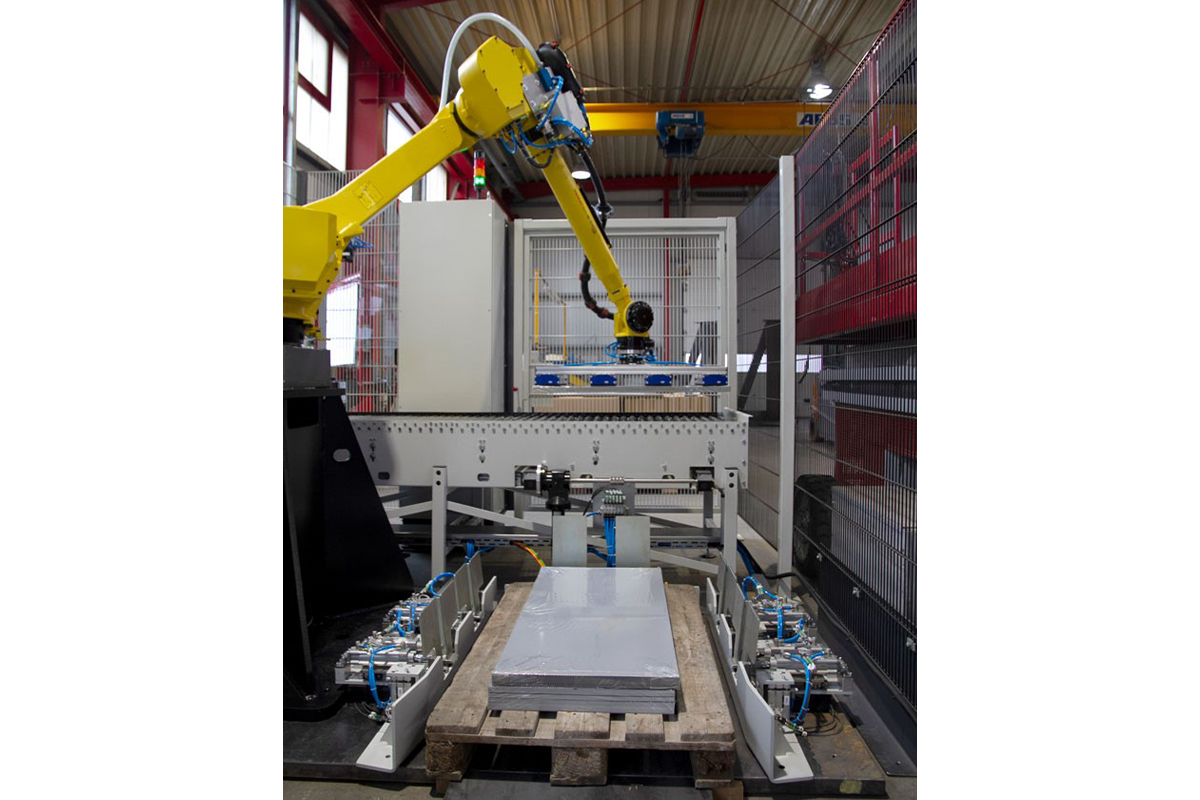
Loading and Stacking Robots
Smart Automation for Precise and Efficient Stacking In today’s industrial environments—with their complex production and ...
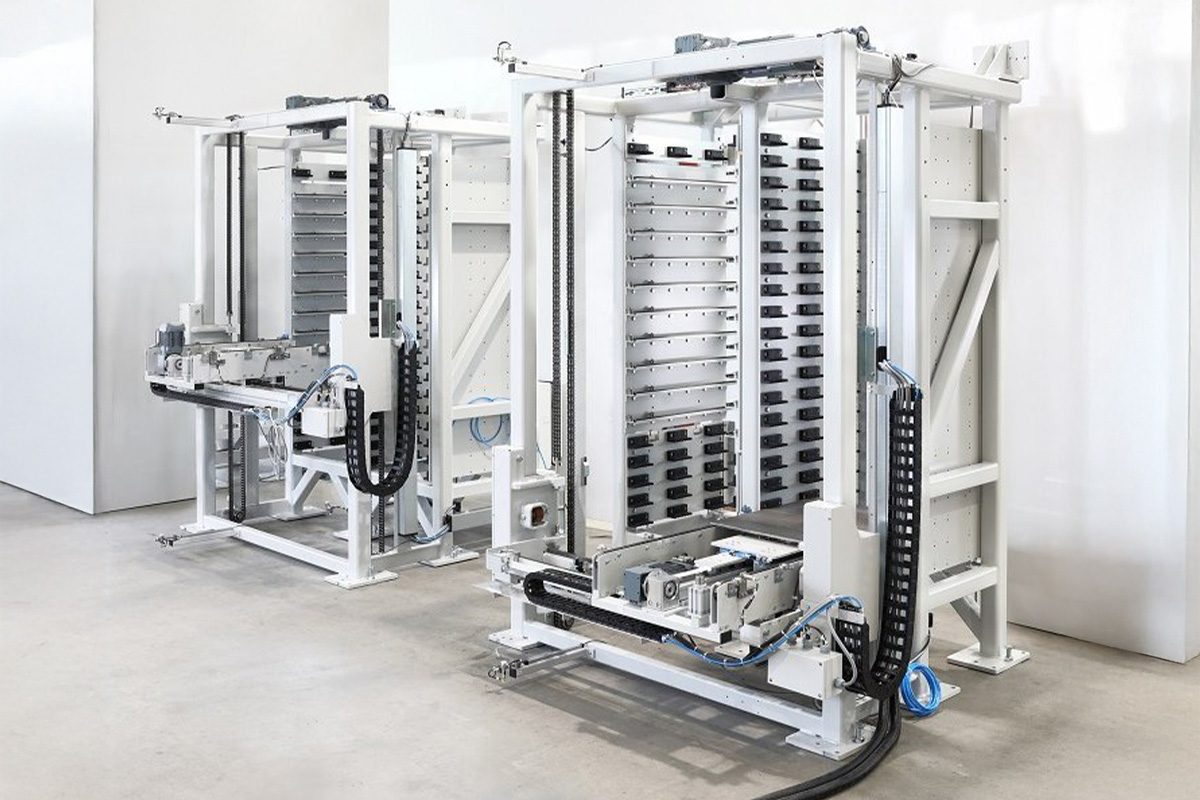
Automated Storage Systems for Multi-Daylight Presses
In high-output production processes involving multi-daylight presses, efficient storage and automation solutions are essential for ...
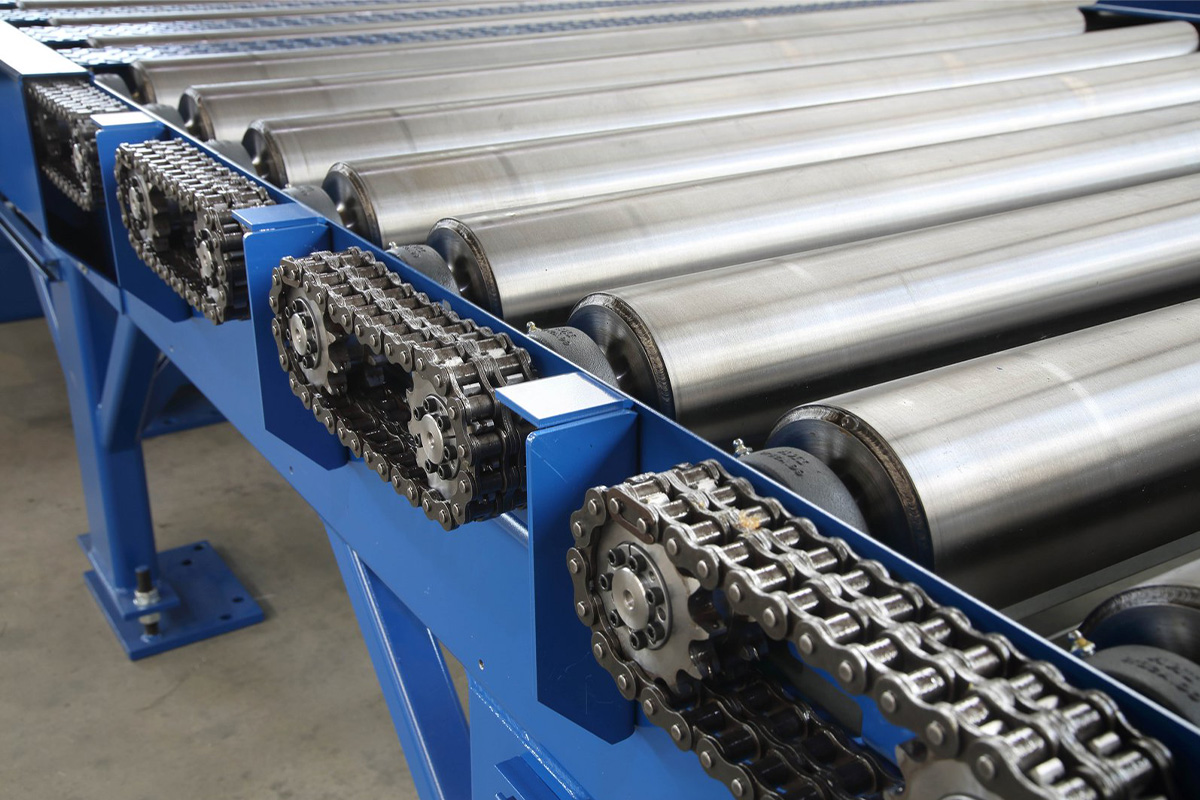
Heavy-Duty Roller Conveyors
Heavy-duty roller conveyors from Rotte are an optional yet integral component of our complete solutions ...
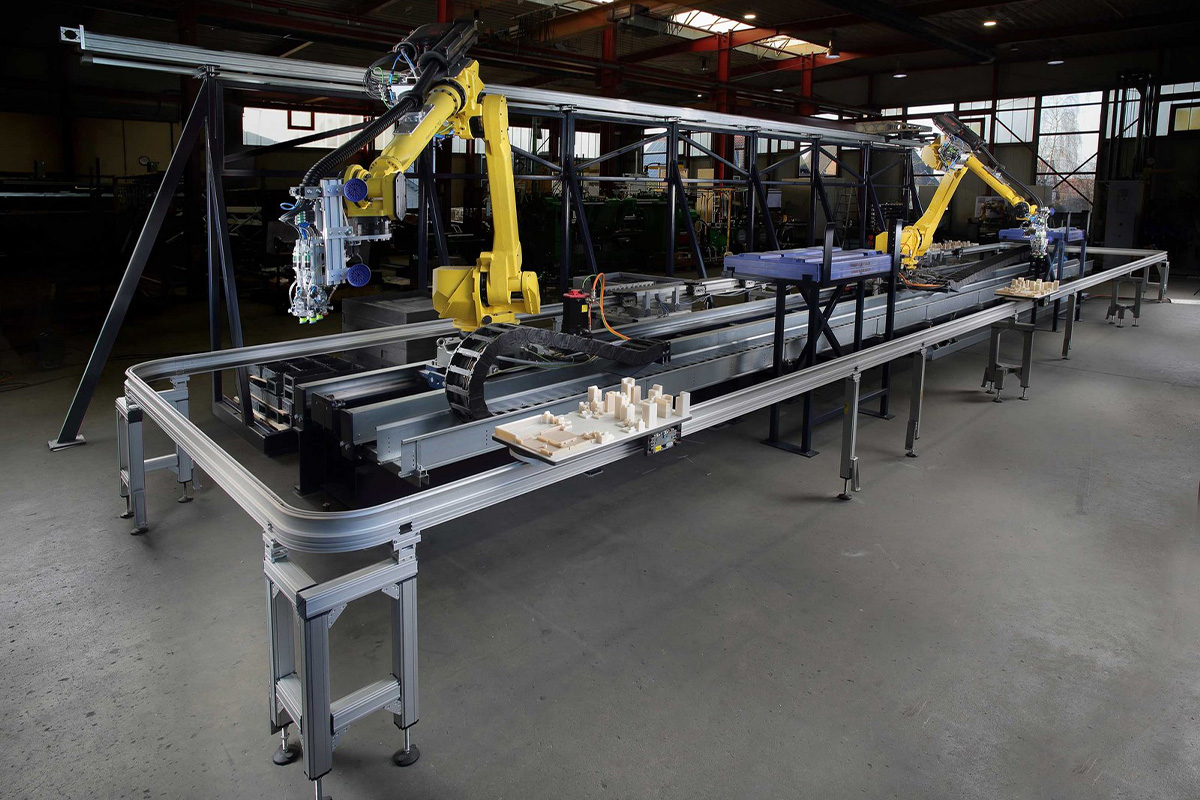
Picking Robots
Robotic Order Picking: Efficient Automation for Precise and Flexible Logistics with Customized Picking Robots In ...